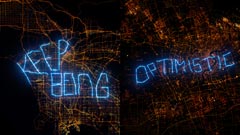
Smart Energy
Two e-cars –
one global message.
By 2025, our innovations in electric car battery materials aim to double the driving range of midsize cars from 300 to 600 km on a single charge. Batteries will be halved in size and their lifespans will be extended. Best of all, drivers could expect to get a full charge in as little as 15 minutes – no longer than it takes to enjoy a quick cup of coffee. There could be as many as 5 to 10 million full battery cars being produced by 2025. BASF’s battery materials innovations will be in many of these electric cars.
We're driving the future of e-mobility
Where will our battery materials take you?
Through chemistry our scientists are constantly developing and introducing sustainable solutions to address some of the planet’s biggest challenges. We believe the continous development of advanced emission control technologies and the increasing demand for electric powered cars will help reduce emissions and increase air quality on a global scale.
Fewer emissions will make our world a better place to live by reducing the impact of air pollution in inner cities and creating a positive effect on the health of the population.
Environmental driven regulations by European, Chinese and other governments around the world, will remain the primary driver for industry growth. We are confident that these regulations combined with our experience in creating unique proprietary solutions for cleaner air, will help address some of the climate change challenges society faces today.“
Deep dive into battery materials research
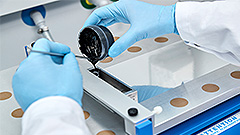
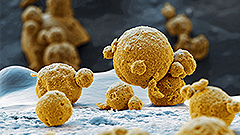
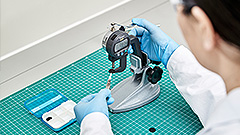
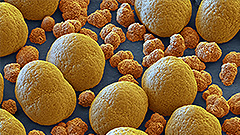
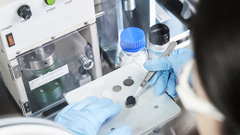

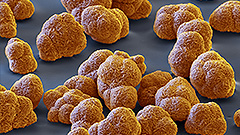
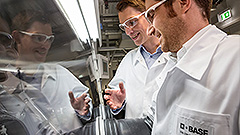